اجزای سیستم هیدرولیک، شیرهای کنترل فشار در هیدروموتور، آکومولاتورها
هیدرولیک از کلمه یونانی”هیدرو” مشتق گردیده است. این کلمه به معنای جریان حرکات مایعات است. در قرون گذشته و مقصود از هیدرولیک فقط آب بوده و البته بعدها عنوان هیدرولیک مفهوم بیشتری به خود گرفت و معنی و مفهوم آن بررسی در مورد بهره برداری بیشتری از آب و حرکت دادن چرخ های آبی و مهندسی آب بوده است.
مفهوم هیدرولیک در این قرن، دیگر مختص به آب نبوده بلکه دامنه وسیع تری به خود گرفته و شامل قواعد و کاربرد مایعات دیگری به خصوص “روغن معدنی” هم است، زیرا آب به علت خاصیت زنگ زدگی، در صنایع نمی تواند به عنوان انرژی انتقال دهنده مورد استفاده قرار گیرد و به علت آن که روغن خاصیت زنگ زدگی ندارد، امروزه در صنایع از آن به خصوص برای انتقال انرژی در سیستم کنترل استفاده بسیار می گردد.
به طور خلاصه می توان گفت: فنی که انتقال و تبدیل نیرو را توسط مایعات انجام دهد “هیدرولیک” نامیده می شود. از آنجایی که هیدرولیک آبی دارای خاصیت زنگ زدگی است، لذا در صنایع از هیدرولیک روغنی هم به خاطر انتقال انرژی در سیستم های کنترل استفاده می شود.
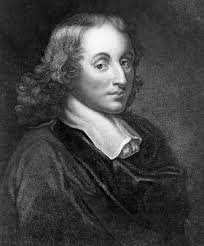
هیدرولیک شاخه ای از فیزیک است که با خواص مکانیکی سیالات سر و کار داشته و موارد استفاده این خصوصیات را در علوم مهندسی بررسی می کند. با وجودی که فقط در حدود ۵۰ سال از عمر این علم می گذرد، ولی آن را نمی توان شاخه تازه ای از علوم دانست و در حقیقت پاسکال، دانشمند فرانسوی در قرن هفدهم اصول و قوانین اساسی این علم را پایه گذاشت.
عدم توانایی در تولید واشرها و تهیه سطوح کاملاً پرداخت شده، شاید دلایل عمده عدم رشد این علم تا قبل از قرن بیستم باشد. با توجه به پیشرفت های چشمگیری که در طی چند دهه گذشته در ساخت مواد در زمینه ها و روش های ماشین کاری حاصل شده است، موارد استفاده از سیالات در کنترل حرکات مختلف روز به روز بیشتر می گردد.
مجموعه پیشرفت های فنون در عصر فضا و کامپیوتر در سال های اخیر سرعت و کارایی سیستم های هیدرولیکی را به گونه ای چشمگیر دگرگون ساخته است، ولی مبانی حاکم بر همه دستگاه ها و اجزای گوناگون همچنان ثابت است. سیستم هیدرولیکی با آب، روغن و یا سیالات دیگر کار می کند. در این سیستم ها در کنار مایع، از هوای فشرده یا برخی گازها و سیالات تراکم پذیر هم می توان استفاده نمود.
نگاهی گذرا بر رشته های مختلف صنعت، نمایان گر گستردگی کاربرد هیدرولیک است. به عنوان مثال در کشاورزی، خودروسازی، صنایع هوایی، راه و ساختمان، صنایع شیمیایی، صنایع دفاعی، صنایع چوب، صنایع دریایی، جابه جایی مواد، ماشین کاری، معدنکاری، بسته بندی، صنعت نفت، صنعت چاپ، لاستیک سازی، راه آهن، نساجی، صنعت فولاد و حتی منازل و مراکز عمومی در مقیاس وسیعی استفاده می شود و روز به روز نیز افزایش می یابد.
مثلاً در صنایع هوایی، خلبان به یاری هیدرولیک، باز و بسته شدن چرخ ها، سکان های عمودی، بالابرها و بالچه ها را مهار می کند. در عملیات ریخته گری تحت فشار، برای ساخت قطعات سبک از آلومینیوم و منیزیم از نیروی هیدرولیک برای بستن قالب ها و تزریق فلز استفاده می شود. بدنه هواپیما را نیز با پرس های کششی که با نیروی هیدرولیک کار می کند شکل می دهند.
کاربردهای هیدرولیک
هیدرولیک فناوری تولید، کنترل و انتقال قدرت توسط سیال تحت فشار است. به طور کلی یک سیستم هیدرولیک چهار کار اساسی انجام می دهد:
- تبدیل انرژی مکانیکی به قدرت سیال تحت فشار به وسیله پمپ ها
- انتقال سیال تا نقاط مورد نظر توسط لوله ها و شلنگ ها
- کنترل فشار، جهت و جریان سیال توسط شیرها
- انجام کار توسط عملگرها
مفاهیم پایه در هیدرولیک
قانون پاسکال
قانون پاسکال پایه هیدرولیک نوین است. این قانون بیان می کند که فشار وارد به هر نقطه از یک مایع محدود، به طور مساوی در تمام جهات منتقل شده و با نیروی مساوی بر روی سطوح مساوی اثر می کند.

قوانین پایه در هیدرولیک
- سیال تحت فشار، همواره مسیر با مقاومت کمتر را برای عبور انتخاب می کند.
- پمپ تولید فشار نمی کند بلکه تولید دبی می کند.
- فشار تنها در برابر مقاومت یک مانع ایجاد می شود.
اصول کلیدی فوق اگر چه ساده به نظر می رسند، ولی پایه و اساس علم هیدرولیک هستند. با داشتن درک صحیحی از این قوانین به راحتی می توان حرکت سیال در خطوط انتقال را دنبال کرده و عملکرد سیستم را تحلیل نمود.
فشار
فشار نتیجه مقاومت در مقابل حرکت سیال است. برای محاسبه ریاضی فشار، نیرو را بر سطح تقسیم می نمایند. واحد فشار “بار” است. در هیدرولیک عملی، معمولاً یک کیلوگرم بر سانتیمتر مربع برابر یک بار است.
تعیین فشار کاری سیستم هیدرولیک
برای تعیین سطح فشار در یک سیستم هیدرولیک، باید در نظر داشت که با بالا بردن فشار می توان از المان های هیدرولیکی کوچکتری برای رسیدن به تناژ مورد نظر، استفاده نمود. همچنین قطر لوله ها را می توان کوچکتر انتخاب نمود در نتیجه، هزینه ساخت سیستم کاهش می یابد. از طرف دیگر با افزایش فشار، دمای روغن در سیستم زودتر افزایش می یابد، نشتی ها بیشتر و اصطکاک و سایش نیز افزایش می یابد، در نتیجه فاصله انجام سرویس ها باید کوتاه تر شود. همچنین نویز و پیک های فشاری نیز افزایش یافته و خواص مطلوب دینامیکی سیستم کاهش می یابد.
عملگر (محرک)
اولین وظیفه یک واحد عملگر، ایجاد حرکت دلخواه یا عمل برای ربات است تا نیروی مورد نیاز صرف شده، یک عمل به صورت فیزیکی انجام دهد. سه منبع برای ایجاد انرژی واحد عملگر وجود دارد:
- نیروی الکتریکی
- نیروی هیدرولیکی
- نیروی نیوماتیک
عملگرها را می توان به پنج دسته تقسیم نمود:
- عملگرهای الکترومکانیکی
- ماشینهای الکتریکی مانند موتورهای AC موتورهای DC و موتورهای پله ای
- عملگرهای پیزوالکتریک
- میکروموتورها
- عملگرهای هیدرولیک و نیوماتیک
اجزاء سیستم های هیدرولیک
هیدرولیک فناوری تولید، کنترل و انتقال قدرت توسط سیال تحت فشار است. یک سیستم عملگر هیدرولیک از اجزاء زیر تشکیل شده است:
- پمپ های هیدرولیکی: جهت به جریان انداختن سیال در سیستم
- شیرهای هیدرولیکی: برای کنترل فشار، جریان و جهت حرکت سیال
- آکومولاتور (انباره های هیدرولیکی)
- فیلتراسیون
- روغن ها و مخازن روغن هیدرولیکی
- سیل های هیدرولیکی (آب بندها)
- اتصالات و شیلنگ های هیدرولیکی
- موتورهای هیدرولیکی
- مبدل ها و اندازه گیرها
- سیلندرهای هیدرولیکی
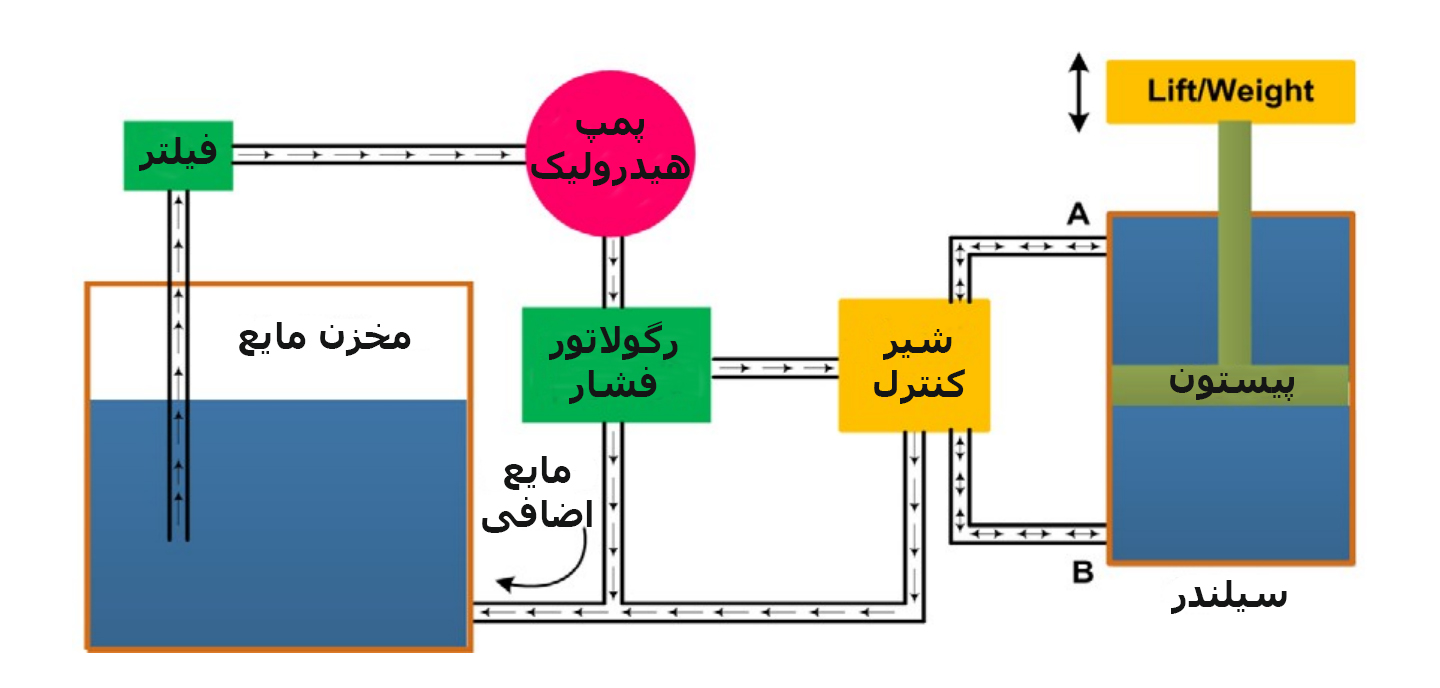
اشکالات عمومی سیستم های هیدرولیکی
۱- کمبود فشار کمبود دبی
۲- زوزه پمپ، سر و صدا و ارتعاشات
۳- حرارت بیش از حد
۴- حرکات غلط عمل کننده ها
۵- استهلاک سریع قطعات
عیب یابی سیستم های هیدرولیک
عیب یابی به معنای یافتن مشکل سیستم بوده و باید طی یک روند منطقی جهت شناسایی قسمت معیوب، اشکالات به صورت مشخص لیست شوند.
– مراحل انجام عیب یابی
– بررسی دستورالعمل تعمیر و نگهداری
– بررسی تاریخچه تعمیر و نگهداری
– انجام بازدید اولیه
– بررسی و تهیه لیست ایرادات مشاهده شده
– محاسبات اولیه
– تعیین عوامل کلی مشکل
– تعیین عوامل اختصاصی بروز مشکل
– انجام آزمایشات مختلف
مزایا و معایب سیستم عملگر هیدرولیک
مزایا:
- داشتن نیرو و توان بالا.
معایب:
- بهترین نوع آن از لحاظ ساخت هم نشتی سیال (روغن) دارد
- روغن های هیدرولیک قابلیت اشتعال دارند
- هزینه بالا برای تهیه پمپ، مخزن، کنترل و اجزاء جانبی
- سر و صدای زیاد
- نگهداری و تعمیر با هزینه بالا و احتیاج به متخصص
- احتیاج به سرویس و چک زمان بندی شده
موتورهای هیدرولیک
کاربرد موتورهای هیدرولیک (Hydraulic Motors) تبدیل فشار یا جریان هیدرولیک از طریق یک شفت به انرژی چرخشی مکانیکی است. موتورها زمانی که به یک خروجی دوار نیاز داشته باشید، به کار گرفته می شوند و راه اندازها (Actuators) برای خروجی خطی مورد استفاده قرار می گیرند. به هر حال در عمل، موتورها بسیار شبیه به پمپ ها هستند. خروجی یک موتور، یک گشتاور و یک سرعت زاویه ای است.(قدرت= گشتاور × سرعت زاویه ای).
موتورها دقیقاً برعکس پمپ ها عمل می کنند، در واقع برخی موتور پمپ ها هر دو نقش را در یک سیستم هیدرولیک ایفا می کنند. (به عنوان یک پمپ یا موتور، بسته به موقعیت سوپاپ های کنترل عمل می کنند). موتورهای هیدرولیک عملگرهایی با دَوَران مداوم هستند که جهت ایجاد گشتاور لازم برای دَوَران بار چرخشی مورد استفاده قرار می گیرند. این عملگرها در انواع دنده ای، پره ای و پیستونی طبقه بندی می شوند.
انتخاب هیدروموتور
برای انتخاب یک هیدروموتور حداقل موارد ذیل باید مشخص گردد:
– حجم جابه جایی روغن بر حسب cm3
– حداکثر دبی مجاز عبوری از موتور و حداکثر سرعت
– ثابت گشتاور برحسب Nm/bar توسط این ثابت می توان مقدار گشتاور موتور را در فشارهای کاری مختلف محاسبه نمود.
– حداکثر گشتاور موتور در اختلاف فشار ماکزیمم بر حسب Nm
کاربرد شیرهای کنترل فشار در مدار هیدروموتور جهت حفاظت از Overload
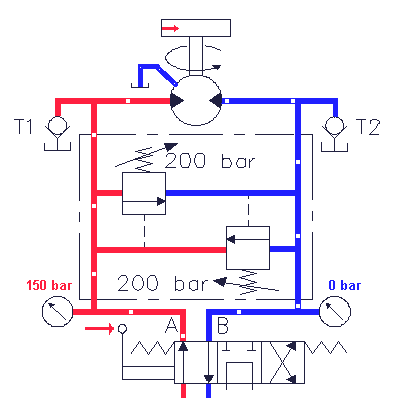
در شکل بالا ملاحظه می کنید که زمانی که از مسیر A جریان برقرار می شود، فشار بار به عنوان مثال ۱۵۰ بار است و جریان از مسیر B خارج می شود. عملگرها یا شیرهای کنترل در این حالت هیچ عملی انجام نداده و هیدروموتور در حال کار بوده و دَوَران می کند. تا اینکه فشار زیاد شده و مثلاً به بیش از ۲۰۰ بار می رسد. در این لحظه یکی از عملگرها که در شکل عملگر پایینی است، عمل نموده و مسیر جریان A به B را مسدود می کند. جریان بار اضافی از مسیر عملگر خارج شده تا اینکه فشار بار اضافی تخلیه شود و به صفر برسد.
تعیین پارامترهای لازم هیدروموتور
در ادامه بحث، برخی پارامترها و فرمول های مربوط به آن ها را در ذیل ذکر می کنیم:
تعیین سرعت دوران و دبی هیدروموتور
(N (rpm)= 1000 × Q (lit/min)/ Vg(cm3
در این رابطه N سرعت دوران هیدرو موتور، Q دبی مورد نیاز و Vg حجم جابه جایی هیدروموتور است.
تعیین توان هیدروموتور
(۹۵۵۰)/(P (Kw) = T (N .m) x N (rpm
در این رابطه P توان هیدروموتور، T گشتاور و N سرعت دوران هیدروموتور هستند. لازم به ذکر است روابط فوق بدون در نظر گرفتن بازده مکانیکی و حجمی ارائه شده است. در عمل مقادیر بازده در گشتاور واقعی و توان مصرفی تأثیر می گذارد.
فیلتراسیون در سیستم هیدرولیک
بسیاری از عملکردهای نامناسب در سیستم هیدرولیک ناشی از روغن های بسیار کثیف است.
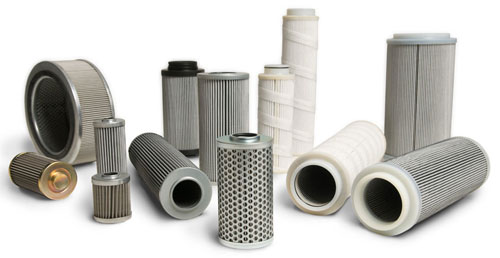
راه های ورود آلودگی و ذرات خارجی به سیستم هیدرولیک
۱- از طریق روزنه های خارجی
۲- از طریق نصب اشتباه
۳- از طریق آلودگی داخلی
۴- از طریق فرسودگی در سیستم هیدرولیک
۵- استفاده از روغن های نامرغوب
۶- تعمیرات اشتباه
مقاله پیشنهادی: بررسی ۹ مدل شیر صنعتی یا ولو
انواع فیلتر در سیستم هیدرولیک
۱- فیلتر خط مکش (Suction line)
۲- فیلتر خط فشار (Pressure line)
۳- فیلتر خط برگشت (Return line)
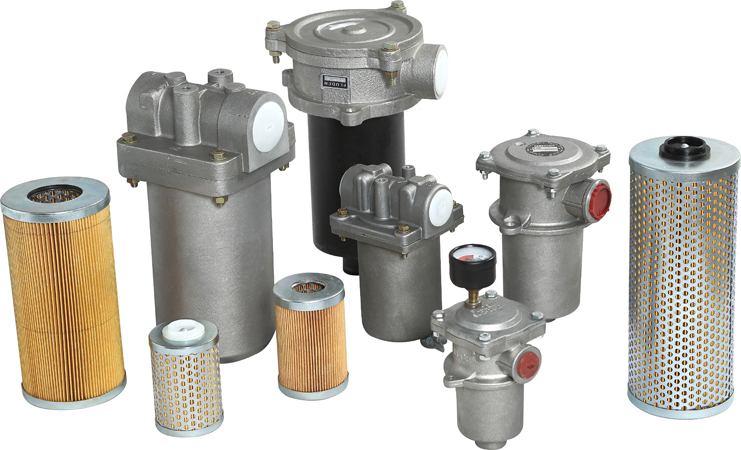
۴- فیلتر بای پس (Offline)
۵- فیلتر فیلر و هواکش (Filler & breather)
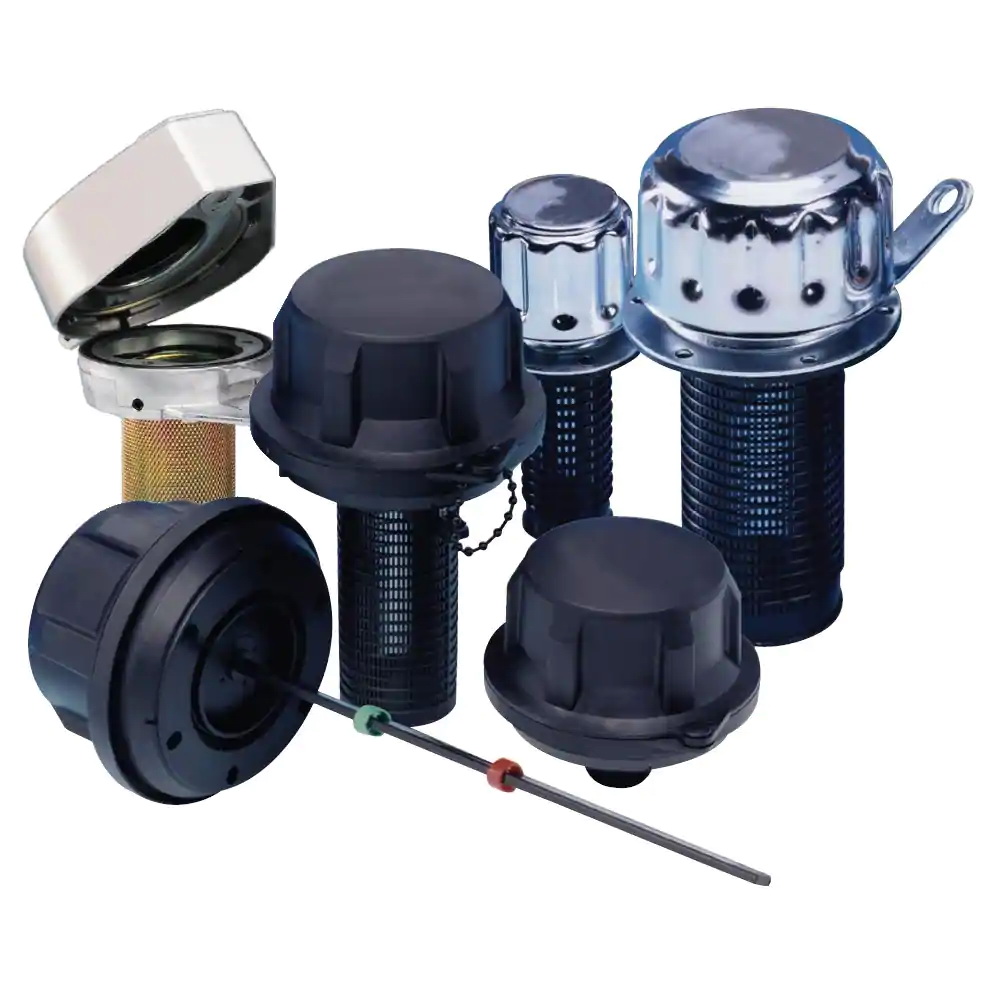
نکته:
مسدود شدن تدریجی صافی ورودی باعث ایجاد موارد ذیل می شود:
١-کاویتاسیون
۲-افزایش صدا
۳-کاهش عمر مفید پمپ
ویژگی های فیلتراسیون خط برگشت
۱-هزینه کم
۲-سرویس ساده
۳-امکان استفاده از نشانگر انسداد
۴-امکان فیلتراسیون ظریف
۵-جلوگیری از ایجاد کاویتاسیون در پمپ
۶-نیاز به شیر بای پس
۷-امکان استفاده از ۲ فیلتر برای کاهش زمان سرویس
جنس فیلترهای هیدرولیک
١- بافت شیشه ای
۲- تشکیل شده از قسمت های جامد گیاهان
٣- تشکیل شده از سیم های بافته شده
ویژگی های یک فیلتر هیدرولیک
١- باید دارای راندمان کاری خوبی باشد.
۲- باید آلودگی ها و کثیفی ها را در خود نگاه دارد و خارج نکند.
۳- باید تحمل فشارهای تفاضلی را دارا باشد.
۴- عمر طولانی در یک سیستم داشته باشد.
۵- هزینه اولیه آن مناسب باشد.
معیارهای طراحی فیلتر هیدرولیک
۱- میزان حساسیت اجزاء بکار گرفته شده در سیستم هیدرولیک به ذرات خارجی
۲- تعیین میزان دبی
۳- اختلاف فشار مجاز
۴- سازگاری مواد فیلتر با روغن مورد استفاده
۵- دمای کاری
۶- ویسکوزیته روغن
در تعیین سایز فیلتر موارد ذیل در نظر گرفته می شوند:
۱- میزان آلودگی محیطی که سیستم در آن قرار دارد.
۲- میزان مراقبت و سرویس سیستم هیدرولیک
۳- دمای کاری روغن
مخزن روغن سیستم هیدرولیک
مخزن روغن از لحاظ کاربردی باید دارای ویژگی های ذیل باشد:
– توانایی ذخیره کردن کل روغن سیستم
– جداسازی هوای موجود در روغن
– ته نشین شدن آلودگی ها در مخزن
– دفع حرارت سیستم مخزن
روغن باید حجم کافی جهت جبران انبساط روغن داخل مخزن داشته باشد. مخازن بهتر است مرتفع و کم عرض ساخته شوند. در مخازن کم عمق، امکان ورود هوا به پورت مکش پمپ وجود دارد.
ابعاد مخزن
ابعاد مخزن روغن در سیستم صنعتی حجم مخزن روغن (lit)= سه تا پنج برابر دبی پمپ ( lit/ min)
ابعاد مخزن روغن در سیستم سیار به ازاء هر ۱۰۰GPM دبی پمپ، حجم مخزن ۳۰~۲۰ gallon
لوله، شلنگ و اتصالات
انواع هدایت کننده های روغن
– لوله های صلب – تیوب (نیمه صلب) – شلنگ های انعطاف پذیر
نکته:
هنگام انتخاب نوع هدایت کننده روغن، نکات ذیل را باید به دقت بررسی نمایید:
– خطوط باید توانایی تحمل فشار کاری محاسبه شده و حداکثر فشار لحظه ای، تا چهار برابر فشار کاری را داشته باشند.
– خطوط انتقال به منظور نصب تجهیزات لازم باید از استحکام کافی برخوردار باشند.
– مسیر روغن باید از نظر ابعاد به اندازه کافی بزرگ باشد تا از افت فشار غیر مجاز (بیش از ۱۰% فشار اولیه) جلوگیری شود و بتوانند کل دبی مورد نیاز را انتقال دهند.
– به منظور کاهش جریان های آشفته و افت های اصطحکاکی، سطوح داخلی خطوط انتقال باید از صافی مناسب برخوردار باشند.
– مواد تشکیل دهنده خطوط انتقال باید با سیال گذرنده از آن ها سازگار باشد.
در بعضی از سیستم های هیدرولیک جهت غلبه بر مشکلات ناشی از به وجود آمدن ضربه و ارتعاشات در خطوط انتقال، استفاده از آکومولاتور توصیه می شود.
آکومولاتورهای هیدرولیکی
آکومولاتورها (انباره ها)
آکومولاتور هیدرولیکی به عنوان یک منبع ثانویه، با ذخیره پتانسیل سیال غیر قابل تراکم (تحت فشار قرار گرفته توسط عامل خارجی) می تواند در هنگام نیاز، مورد استفاه قرار گیرد. به منظور ذخیره سازی انرژی از مکانیزم های وزنه ای، فنری و یا گازی استفاده می شود.

این آکومولاتور به سه دسته کلی زیر تقسیم می گردد:
١- پیستونی
۲- دیافراگمی
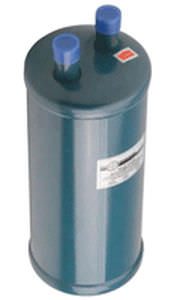

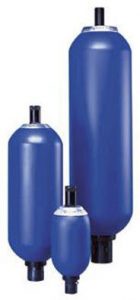
۳- کیسه ای
آب بندهای هیدرولیکی (سیلینگ های دینامیکی)
برای نگهداری روغن تحت فشار در سیستم هیدرولیک، استفاده از آب بند ضرورت دارد. آب بندها علاوه بر آن از ورود گرد و خاک به داخل سیستم ممانعت بعمل می آورند. آب بندها در عین سادگی در حین کار خیلی پیچیده بوده و جزء قطعات دقیق به حساب می آیند.
سیلینگ های دینامیکی بین سطوح قطعاتی که نسبت به هم دارای حرارت هستند قرار گرفته و نشتی و روانکاری را کنترل می نماید. در بسیاری از موارد، طراحی سیلینگ ها به گونه ای است که از ورود ذرات اضافی و مواد خارجی نیز جلوگیری به عمل می آورد.
کاربرد آب بندهای هیدرولیکی
آب بندها بر اساس زمینه کاربرد به دو دسته اصلی تقسیم می گردند:
– آب بندهای استاتیک که برای آب بندی قطعات ثابت بکار می روند.
– آب بندهای دینامیک که برای آب بندی قطعات متحرک کاربرد دارند.

در آب بندهای دینامیک، کمی نشست روغن برای روغن کاری آب بند منظور شده ولی این موضوع در مورد آب بندهای استاتیک قابل قبول نیست.
انواع آب بندهای هیدرولیکی
آب بندها را براساس شکل ظاهری به صورت زیر تقسیم می نمایند:
١– پکینگ های فنجانی (packing cup)
۲- پکینگ های فلنجی شکل (flange packing)
۳- پکینگ های یو شکل (u- packing)
۴- پکینگ های وی شکل (v–packing)
۵- آب بندهای فنری یا کاسه نمدی (spring –loaded lip seal)
۶- اورینگ ها (o- ring)
۷- پکینگ های تراکمی (packing compression)
۸- آب بندهای مکانیکی (mechanical seal)
۹- آب بندهای فلزی باز شونده و باز نشونده (expanding & non – expanding)
پمپ هیدرولیکی
پمپ به عنوان قلب سیستم هیدرولیک، که انرژی مکانیکی را از یک منبع خارجی اخذ و به سیال مایعی که از آن عبور می کند، انتقال می دهد. در نتیجه انرژی سیال پس از خروج از پمپ افزایش می یابد. یک پمپ هیدرولیکی، انرژی مکانیکی را از طریق عامل ایجاد فشار (پیستون، چرخ دنده، پره و غیره) به سیال منتقل می نماید.
انواع پمپ های هیدرولیکی
پمپ ها در صنعت هیدرولیک به دو دسته کلی تقسیم می شوند:
١- پمپ های با جابه جایی غیر مثبت (پمپ های دینامیکی)
۲- پمپ های با جابه جایی مثبت

مقاله پیشنهادی : ساختار سیستم پنوماتیک
نکاتی در مورد پمپ های با جابه جایی غیر مثبت

۱- توانایی مقاومت در فشارهای بالا را ندارند و به ندرت در صنعت هیدرولیک مورد استفاده قرار می گیرند و معمولاً به عنوان انتقال اولیه سیال از نقطه ای به نقطه دیگر به کار گرفته می شوند.
۲- برای سیستم های فشار پایین و جریان بالا که حداکثر ظرفیت فشاری آن ها ۲۵۰psi ~۳۰۰۰psi است استفاده می شوند.
پمپ های گریز از مرکز (سانتریفوژ) و محوری، نمونه کاربردی پمپ های با جابه جایی غیر مثبت هستند.

نکاتی در مورد پمپ های با جابه جایی مثبت
در این پمپ ها به ازای هر دور چرخش محور، مقدار معینی از سیال به سمت خروجی فرستاده می شود و توانایی غلبه بر فشار خروجی و اصطحکاک را دارد. این پمپ ها مزیت های بسیاری نسبت به پمپ هایی با جابه جایی غیر مثبت دارند، مانند:
- ابعاد کوچکتر
- بازده حجمی بالا
- انعطاف پذیری مناسب
- توانایی کار در فشارهای بالا.
- توانایی غلبه بر فشار خروجی
- ابعاد کوچکتر، بازده حجمی بالا و طراحی آسان
- انعطاف پذیری مناسب و توانایی کار در فشارهای بالا
از معایب این پمپ ها می توان به کاهش بازده آن ها در اثر فرسایش قطعات به دلیل اصطکاک و خوردگی نام برد.
انواع پمپ جابه جایی مثبت (دبی ثابت و متغیر)
پمپ دنده ای
در پمپ های دنده ای، دَوَران یکی از چرخ دنده ها به وسیله سیستم محرک تأمین می گردد. پمپ هایی دنده ای بدلیل برخورداری از طراحی ساده، ابعاد کوچک و فشرده و قیمت ارزان، در سیستم های هیدرولیک دارای مصرف عام هستند که به دو دسته تقسیم بندی می شوند:
- دنده خارجی
- دنده داخلی
۱- دنده خارجی
با توجه به دورهای بالای پمپ که تا ۲۷۰۰rpm می رسد پمپاژ بسیار سریع انجام می شود، این مقدار در پمپ های دنده ای با جابه جایی متغییر می تواند ۷۵۰rpm ~ 1750rpm باشد.
پمپ های دنده ای برای فشارهای (تا ۲۰۰ کیلوگرم بر سانتی متر مربع) ۳۰۰۰Psi طراحی شده اند که البته اندازه متداول آن ۱۰۰۰psi است.

۲- دنده داخلی
باید توجه داشت که این دنده ها همواره روغن کاری شده که خشک عمل ننمایند و اگر مایع پمپ شونده خاصیت روغن کاری داشته باشد، عمر پمپ دورانی زیاد می شود. این پمپ ها برای ظرفیت هایی نسبتاً کم با فشار متوسط موارد استفاده زیاد دارند.

پمپهای پرهای
به طور کلی پمپ های پره ای به عنوان پمپ های فشار متوسط مورد استفاده قرار می گیرند. سرعت آن ها معمولاً ۱۲۰۰rpm ~ 1750rpm بوده و بازده حجمی این پمپ ها ۹۰%~۸۵% است. اغلب این پمپ ها آرام و بی سر و صدا کار می کنند، از مزایای جالب این پمپ ها این است که در صورت بروز اشکال در ساختمان پمپ، بدون جدا کردن لوله های ورودی و خروجی قابل تعمیر است.
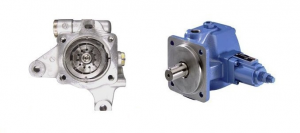
پمپ های پیستونی
این پمپ تشکیل شده است از سیلندر، پیستون، شیر ورودی و شیر خروجی. سطح پیستون بوسیله دسته ای بر روی چرخ دواری قرار گرفته و در جهت بالا و پایین حرکت می کند.
هنگام حرکت پیستون به طرف بالا دریچه A در اثر مکش و برگشت جریان از مجرای خروجی بسته شده و در اثر مکش دریچه B باز و مایع به درون محفظه پمپ مکیده می شود. هنگامی که پیستون به طرف پایین حرکت می نماید، دریچه B بسته شده و دریچه A باز می گردد و سیال محبوس در محفظه و تحت فشار پیستون به مجرای خروجی انتقال می یابد. تکرار این عمل سبب انتقال سیال از یک محل به محل دیگر می گردد.

پمپ های پیستونی محوری با محور خمیده
در این پمپ ها دوران محور، موجب رفت و برگشت پیستون ها می شود. میله های پیستون توسط Ball & socket joints به فلنج محور محرک متصل هستند و یک اتصال یونیورسال، بلوک سیلندر را به محور محرک مرتبط می نماید.
با تغییر زاویه از صفر تا ۳۰ درجه، دبی خروجی پمپ تغییر می کند. در انواع جابه جایی ثابت، معمولاً در زوایای °۲۳ یا °۳۰ عمل می کند. زاویه انحراف پمپ پیستونی با محور خمیده و جابه جایی متغییر بوسیله مکانیزم دستی قابل تنظیم هستد.
پمپ پیستونی محوری با صفحه زاویه گیر (swash plate)
در این نوع پمپ ها، محور بلوک سیلندر و محور محرک در امتداد خط مرکزی قرار دارند. به هنگام چرخش بلوک سیلندر، پیستون ها به دلیل پیروی از وضعیت صفحه زاویه گیر، حرکت رفت و برگشتی می نمایند. در نوع جابه جایی متغیر، وضعیت صفحه زاویه گیر بوسیله مکانیزم های دستی، سرور کنترل و سیستم جبران کننده فشار تنظیم می گردد. حداکثر زاویه مربوط به صفحه زاویه گیر ۱۷٫۵۰ درجه است.
میزان جابجایی در پمپ ها
پمپ ها با جابه جایی مثبت از نظر میزان جابه جایی:
١- پمپ ها با جابه جایی ثابت
۲- پمپ های با جابه جایی متغیر در انتخاب پمپ های با جابه جایی ثابت، موارد ذیل باید در نظر گرفته شود:
١- قطر دهانه های پمپ
قطر دهانه ورودی برای اتصال به خط مکش و دهانه خروجی برای اتصال به خط فشار، باید ارائه گردد و برای مثال اعداد Pipe Connection مشخص گردد. این مشخصه تحت عنوان ۳/ ۴ , ۱ / ۲ , ۲, ۱۱ / ۲ , ۱۱ / ۴ , ۱ اینچ می تواند باشد.
۲- فشار کاری در خروجی پمپ
این مشخصه تحت عنوان Operating Pressure- Outlet و با واحد barارائه می شود و نشانگر ماکزیمم فشاری است که پمپ قادر به تأمین آن خواهد بود. البته لازم به یادآوری است که پمپ ها ایجاد جریان می کنند و قرار گرفتن یک مانع در برابر این جریان، باعث ایجاد فشار می گردد. فشار کاری معمول برای پمپ های دنده ای به صورت ۲۵۰ , ۲۲۵ , ۲۰۰ , ۱۷۵ , ۱۵۰ , ۱۰۰ , ۵۰ , ۱۰ بار است.
٣- فشار کاری در ورودی پمپ
این مشخصه تحت عنوان Operating Pressure- Outlet و با واحد bar ارائه می شود و نشانگر محدوده قابل قبول برای اعمال فشار در ورودی پمپ است. ورودی پمپ را به خط مکش وصل می نمایند که توسط آن روغن از منبع به سمت پمپ مکیده می شود. در حقیقت، مکش فقط یک کلمه است که برای نشان دادن سمت روغن گیری پمپ بکار می رود. اصولاً مایعات قابل کشیده شدن نیستند بلکه فقط با نیروی فشار خارجی هل داده می شوند.
قدرت کشش یک پمپ بستگی به میزان اختلاف فشار سمت مکش پمپ و فشار هوای روی سطح مایع دارد. بنابراین حتی اگر یک پمپ بتواند تولید خلأ مطلق کند، مقدار ارتفاع کشش مایع آن از حداکثر نیروی فشار جو تجاوز نمی کند و حد نهایی ارتفاع کشش را حداکثر فشار وارده بر سطح مایع از طرف هوای بیرون تعیین می کند و به قدرت پمپ بستگی ندارد، از این رو ارتفاع مکش پمپ ها محدود بوده و هرچه پمپ نزدیکتر به سطح مایع نصب شود، مایع راحت تر و آسان تر به سمت پمپ رانده می شود و احتمال ایجاد کاویتاسیونکمتر می شود.
۴- سرعت دَوَران پمپ
میزان دبی حجمی روغن که توسط پمپ ایجاد می گردد، تابع سرعت دوران آن است. این سرعت برای پمپ های مختلف، عددی متغیر است.
۵- حجم جابه جایی روغن
هر پمپ بسته به سرعت دوران خود به ازاء هر دور چرخش چرخ دنده ها، مقدار معینی از روغن را جابه جا می کند. واحدی که برای بیان حجم جابه جایی بکار می رود معمولا cm/ rev است. حجم جابه جایی، عددی است که تابع مشخصات ابعادی چرخ دنده ها مانند قطر دنده، مدل و سرعت دوران پمپ بوده . رنج معمول حجم جابه جایی بین ۳٫۵ و ۱۰۰ لیتر بر دور خواهد بود.
۶- درجه ویسکوزیته
روغنی که پمپ می تواند به صورت مؤثر منتقل نماید باید دارای درجه چسپندگی به خصوصی باشد. رنج ویسکوزیته معمول برای پمپ های دنده ای ۳۰۰-۵ سانتی استوک است.
نحوه انتخاب پمپ های هیدرولیک
اولین مرحله در انتخاب مدار تغذیه و تعیین پمپ مناسب برای یک کاربرد معین در سیستم های هیدرولیک، بررسی میزان فشار جریان در مدار است. ابتدا منحنی های جریان و فشار در یک سیکل زمانی باید بررسی شود. سپس همزمانی مصرف در المان های مختلف تعیین گردد. بدین نحو حداکثر جریان مورد نیاز مشخص می گردد. برای تعیین یک مدار تغذیه مناسب به موارد ذیل باید توجه نمود:
۱- در سایزینگ پمپ ها در عمل باید حدود (۱۰%) به دبی تعیین شده از طریق محاسبات تئوریک اضافه نمود.
۲- در انتخاب شیر اطمینان (فشار شکن)، فشار تنظیمی باید (۱۰%) بیشتر از فشار کاری سیستم باشد.
هر دو مورد ۱ و ۲ باعث می شود توان بیشتری در سیستم هیدرولیک تزریق شود. با تعیین فشار کاری و دبی، مصرف روغن مورد نیاز برای الکتروموتور گرداننده پمپ در سیستم، با استفاده از فرمول ۶۰۰/ [(P (KW) = [Q (lit/min) x p (bar محاسبه می شود.
سیستم محرک پمپ
در بیشتر مواقع برای به حرکت در آوردن پمپ و تأمین توان لازم از الکتروموتور یا موتورهای احتراقی (دیزلی یا بنزینی) استفاده می شود. موتورهای احتراقی معمولاً در سیستم های موبیل کاربرد دارد.
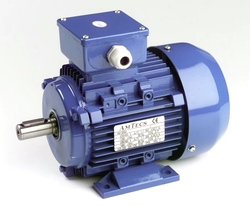

انتقال قدرت به پمپ، گاهی مستقیم از گیربکس اصلی وسایل نقلیه انجام می شود. در ماشین آلات بزرگ مانند جرثقیل های موبیل، از یک دیزل و یک گیربکس پخش قدرت استفاده می شود. گیربکس همزمان قدرت تولیدی را به چند پمپ منتقل می نماید.
اما در سیستم های صنعتی تأمین قدرت توسط الکترو موتور صورت می گیرد. در سیستم های کوچک از موتورهای تک فاز و در سیستم های بزرگ از موتورهای سه فاز استفاده می شود. کوپلاژصحیح موتور و پمپ، از نکات بسیار مهم در ساخت یونیت های هیدرولیک است. اتصال پمپ به موتور از طریق کوپلینگ انجام می شود. پمپ های هیدرولیک را می توان از طریق پایه مستقل نیز مستقر نمود.
در هر صورت باید به یاد داشت انحراف شفت موتور و پمپ و کوپلاژ غلط به سرعت باعث خرابی یاتاقان های آنها شده و ایجاد سر و صدا و گرمای بیش از حد در پمپ می نماید، از این رو لازم است کوپلاژ توسط تکنسین های مجرب و با رعایت تلرانس های دقیق انجام شود.
طراحی و آنالیز مدار هیدرولیک
طراحی و آنالیز مدارهای هیدرولیک از فنونی است که نیاز به درک عمیق و شناخت کامل اجزاء و المان های هیدرولیک دارد. طراح با شناخت نحوه کارکرد عناصر مختلف و نحوه ارتباط آنها با توجه به نیاز سیستم مدار مناسب را طراحی می نماید.

برای یک عملکرد خاص می توان چندین طرح مختلف ارائه نمود. طراحان مجرب با شناخت کاملی که از مدارهای متداول هیدرولیک دارند، اقدام به طراحی سیستم های جدید می نمایند. مدارها به دو گروه مدارهای متداولو مدارهای خاصطبقه بندی می شوند. تسلط به مدارهای پایه راه گشای طراحی مدارهای پیچیده خواهد بود.
مقاله پیشنهادی: آشنایی با سیستم ها و تجهیزات ابزار دقیق
مدارهای متداول (پایه) هیدرولیک
در لیست زیر به تعدادی از مدارهای پایه اشاره می نماییم:
مدار کنترل حرکت سیلندر یک کاره
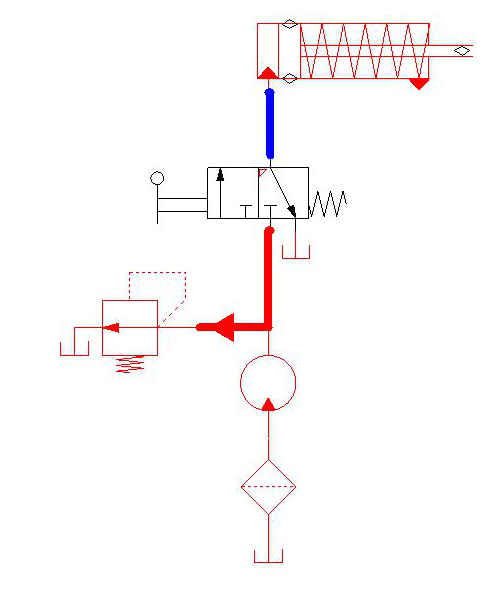
مدار کنترل حرکت سیلندر دو کاره
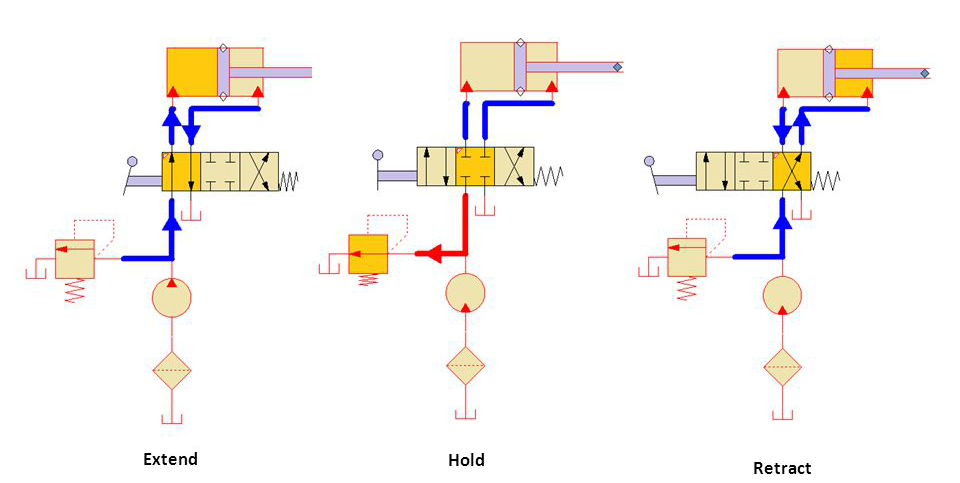
سیستم هیدرولیک دو پمپی

سیلندر هیدرولیک همراه با کانتر بالانس
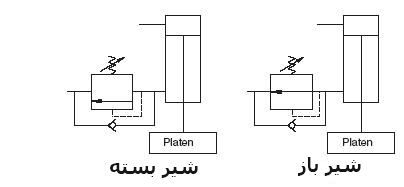
مدار حرکت ترتیبی سیلندرهای هیدرولیک
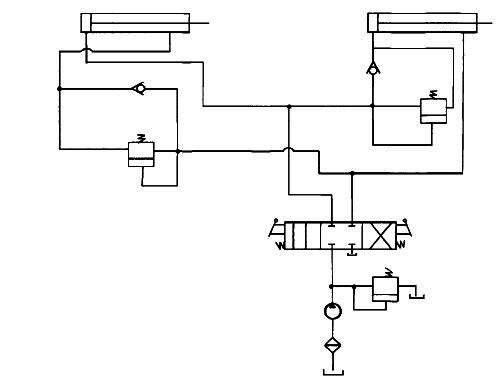
مدار قفل آن سیلندر
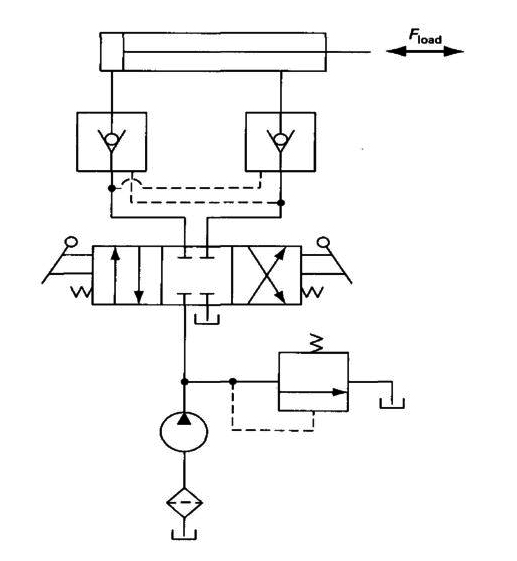
مدار رفت و برگشت اتوماتیک سیلندر

حرکت سینکرون سیلندرهای هیدرولیک

سیستم ترمز هیدروموتور
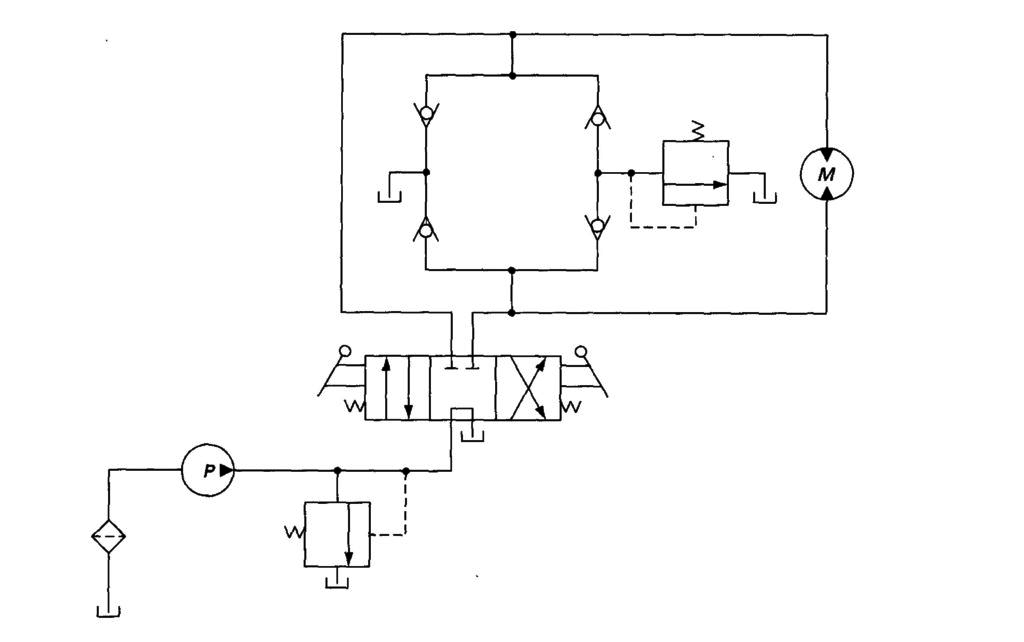
کنترل سرعت موتور هیدرولیک
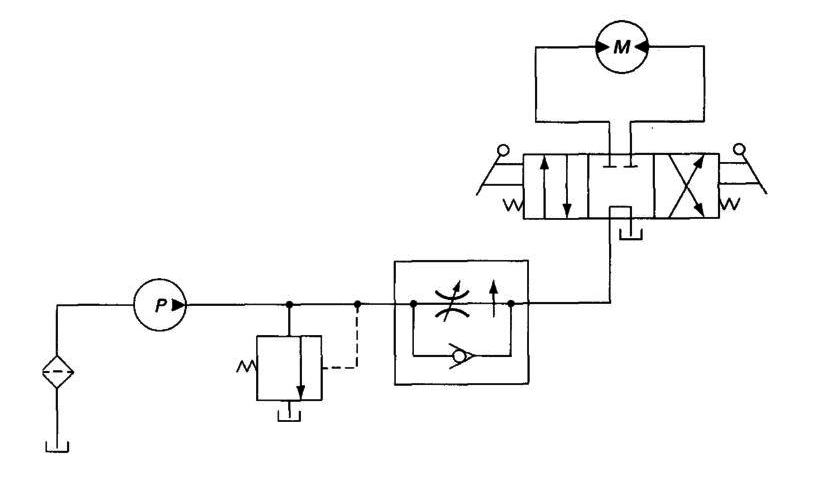
مدار کنترل سرعت سیلندر هیدرولیک

– کنترل سرعت از طریق جریان ورودی
– کنترل سرعت از طریق جریان خروجی
– راه اندازی هیدروموتور
– مدار بی بار کننده پمپ
– مدار سوئیچ فشاری
– مدار تأمین کننده در سطح فشار کنترلی
– مدار شامل فلودیوایدر
– مدار شیر یک طرفه را به عنوان مدارات پایه می نامند.
مدارهای خاص
– مدار شامل شیرهای پروپورشنال و سروو
– مدار متشکل از چند پمپ
– مدار سیستم انتقال قدرت هیدروستاتیک
– مدار هیدرولیک شامل آکومولاتور
مدار سیستم لودر
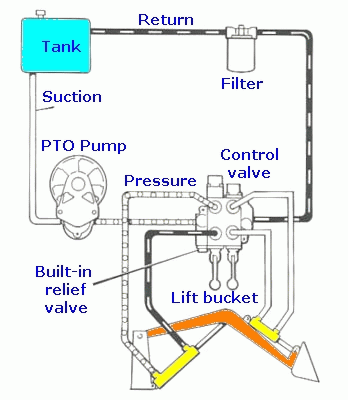
مدار سیستم وینچ
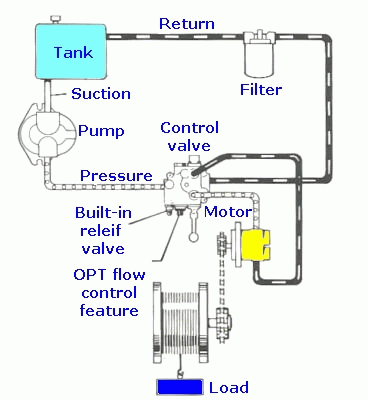
مدار سیستم چوب خرد کن

سیلندر های هیدرولیک
سیلندرهای هیدرولیک، جریان سیال تحت فشار را به حرکت خطی میله پیستون تبدیل می کنند. سیلندرهای هیدرولیک در دو مدل یک کاره و دو کاره تولید می شوند. در نوع یک کاره، برگشت به موضع اولیه توسط فنر یا نیروی سنگینی بار صورت می پذیرد، ولی در نوع دو کاره، عمل رفت و برگشت تحت کنترل سیال هیدرولیکی انجام می شود.
انتخاب سیلندرهای هیدرولیک
در انتخاب سیلندرهای هیدرولیک موارد ذیل باید در نظر گرفته شود:
- حداکثر فشار کاری سیستم
- قطر پیستون و میله پیستون
- نیروی سیلندر
- حداکثر نیروی سیلندر
- طول کورس سیلندر
- حداکثر سرعت سیلندر
- نحوه نصب سیلندر
- وجود ضربه گیر
- نوع و کاربرد سیلندر
مشکلات اساسی در ارتباط با سیلندرهای هیدرولیک
- بارگذاری غیر محوری
- نصب نامناسب
- خم شدن میل پیستون
- محاسبات نادرست در شتاب گیری و کاهش سرعت بار
- بارهای ضربه ای سنگین
- نشتی های داخلی و خارجی
- تقویت فشار ناخواسته
- سرعت و ترتیب حرکت نادرست
- خراب شدن سریع تجهیزات داخلی سیلندر نظیر O-Ring ها و واشرها
محاسبات نیرو و سرعت سیلندر
برای دستیابی به نیروی مورد نظر ابتدا سطح فشار کاری باید تعیین گردد. برای مثال فشار bar) ۱۲۰) در صنعت بسیار متداول است. با توجه به فشار کاری و نیروی مورد نیاز، سطح مقطع سیلندر از رابطه زیر تعیین می گردد.
(F(Kgf)=P(bar) xA(cm2
مدار کنترل سرعت سیلندر
سیستم هایی طراحی شده اند که می توانند سرعت حرکت سیلندر و پیستونآن را کنترل کنند. از جمله می توان به موارد زیر اشاره نمود:
- مدار کنترل جریان سرریز Bleed off circuit
- مدار اندازه گیری مقدار جریان ورودی یا کنترل در دهانه تغذیه Meter-in circuit
- مدار اندازه گیری مقدار جریان خروجی یا کنترل در دهانه تخلیه Meter-out circuit
- مدار تغذیه متغییر Variable feed
- پمپ حجم متغییر Variable-volume pump
- مدار حرکت سنکرون سیلندر
راه اندازی سیلندر
در راه اندازی سیلندرهای نو به یاد داشته باشید که هوای محبوس در سیلندر باید خارج شود. خروج هوا معمولاً پس از چند بار حرکت به جلو و عقب انجام می شود. تا زمانی که هوا در سیلندر محبوس باشد امکان حرکت ناگهانی و ناخواسته وجود دارد. بعضی از سیلندرها دارای پیچ هواگیری هستند. توسط این پیچ به راحتی هوای داخل سیلندر خارج می شود.
مقاله پیشنهادی: انواع پی ال سی (PLC) و ساختار آن
در صورتی که سوالی در خصوص مطالب بیان شده دارید می توانید در قسمت نظرات از ما بپرسید یا با ارائه پیشنهادات خود، ما را در بالا بردن کیفیت مقالات یاری کنید.
میانگین امتیازات ۵ از ۵
از مجموع ۳ رای
سوالات متداول
علم هیدرولیک چیست؟
هیدرولیک شاخه ای از فیزیک است که با خواص مکانیکی سیالات سر و کار داشته و موارد استفاده این خصوصیات را در علوم مهندسی بررسی می کند. با وجودی که فقط در حدود ۵۰ سال از عمر این علم می گذرد، ولی آن را نمی توان شاخه تازه ای از علوم دانست و در حقیقت پاسکال، دانشمند فرانسوی در قرن هفدهم اصول و قوانین اساسی این علم را پایه گذاشت. عدم توانایی در تولید واشرها و تهیه سطوح کاملاً پرداخت شده، شاید دلایل عمده عدم رشد این علم تا قبل از قرن بیستم باشد. با توجه به پیشرفت های چشمگیری که در طی چند دهه گذشته در ساخت مواد در زمینه ها و روش های ماشین کاری حاصل شده است، موارد استفاده از سیالات در کنترل حرکات مختلف روز به روز بیشتر می گردد. مجموعه پیشرفت های فنون در عصر فضا و کامپیوتر در سال های اخیر سرعت و کارایی سیستم های هیدرولیکی را به گونه ای چشمگیر دگرگون ساخته است، ولی مبانی حاکم بر همه دستگاه ها و اجزای گوناگون همچنان ثابت است. سیستم هیدرولیکی با آب، روغن و یا سیالات دیگر کار می کند. در این سیستم ها در کنار مایع، از هوای فشرده یا برخی گازها و سیالات تراکم پذیر هم می توان استفاده نمود.
برای انتخاب پمپ هیدرولیک باید به چه نکاتی توجه کنیم؟
اولین مرحله در انتخاب مدار تغذیه و تعیین پمپ مناسب برای یک کاربرد معین در سیستم های هیدرولیک، بررسی میزان فشار جریان در مدار است. ابتدا منحنی های جریان و فشار در یک سیکل زمانی باید بررسی شود. سپس همزمانی مصرف در المان های مختلف تعیین گردد. بدین نحو حداکثر جریان مورد نیاز مشخص می گردد. برای تعیین یک مدار تغذیه مناسب به موارد ذیل باید توجه نمود: ۱- در سایزینگ پمپ ها در عمل باید حدود (۱۰%) به دبی تعیین شده از طریق محاسبات تئوریک اضافه نمود. ۲- در انتخاب شیر اطمینان (فشار شکن)، فشار تنظیمی باید (۱۰%) بیشتر از فشار کاری سیستم باشد. هر دو مورد ۱ و ۲ باعث می شود توان بیشتری در سیستم هیدرولیک تزریق شود. با تعیین فشار کاری و دبی، مصرف روغن مورد نیاز برای الکتروموتور گرداننده پمپ در سیستم محاسبه می شود.